In the light of the largest economic crisis since the Second World War and the subsequent rapid recovery which followed it, the course of economic development in recent years has demonstrated that production guarantees a stable and competitive economy.
However, volatile markets, new market participants active on a global level, short-lived sales markets, customised products and difficult production processes demand even more flexible production systems and personnel with a greater capacity to respond to these challenges. Added to this, a high level of productivity and quality must also be maintained.
Production secures prosperity, employment and, ultimately, the future for all of us. During times in which we see relocation to low-wage countries, the European economy asserts itself through flexibility, quality and stability. This applies in particular to the winding industry. The principles of lean production have come to prevail in recent years in the winding industry, with flexibility increasing as a result and contributing to major successes in terms of productivity and delivery readiness. Production currently faces another upheaval. The extensive introduction of information and communication technology, and its networking with the internet of things, services and data enabling real-time production, is propagated under the eye-catching term of Industry 4.0. Autonomous objects, mobile communication and real-time sensors enable the realisation of completely new applications involving decentralised control and ad-hoc design of processes.
The need to be able to react quickly and flexibly to customer demands, and produce high numbers of variants efficiently in low batch sizes will increase, once again raising the level of competitiveness. New forms of customer-integrated business processes will become possible and also make inroads into the winding industry, which is governed by many current industrial megatrends.
The possibilities and challenges which characterise Industry 4.0 are also an important issue at the SynFlex Group. SHWire has already implemented integration of the FIT process monitoring platform on all production lines as the central communication module of the SHWire operational acquisition system.
The FIT process monitoring platform records all relevant machine, product and quality parameters in real time. It evaluates these and then provides the machine and machinery operators with the results. At the heart of the online data acquisition system is an innovative high-voltage failure rate tester, the HFZ, which was developed by Schwering & Hasse.
Thanks to FIT, SHWire far exceeds the level of random quality tests required by the DIN standard: Destructive offline testing is replaced by a non-destructive 100 % inline test.
The high-voltage failure rate tester reliably, reproducibly and quantitatively measures the strength and frequency of insulation fluctuations. The HFZ therefore tests the high-voltage failure rate on 100% of the delivered production quantity.
During data processing, FIT ensures complete and immediate transparency of the current status of all production lines in real time. FIT data are completely documented and ensure complete traceability.
The traceability of machine, product and process data permits the secure limitation of faults if the need arises. The FIT system is increasingly replacing humans as the element of uncertainty in the production of enamelled wires, enabling the identification and correction of deviations from the ideal state of production as quickly as possible.
Thanks to the 100 % HFZ test, every customer can be sure of receiving products that conform to prescribed specifications over the entire length delivered. At SHWire, every centimetre is really tested with regard to insulation weak points. Living Industry 4.0 through innovative projects at the SynFlex Group.
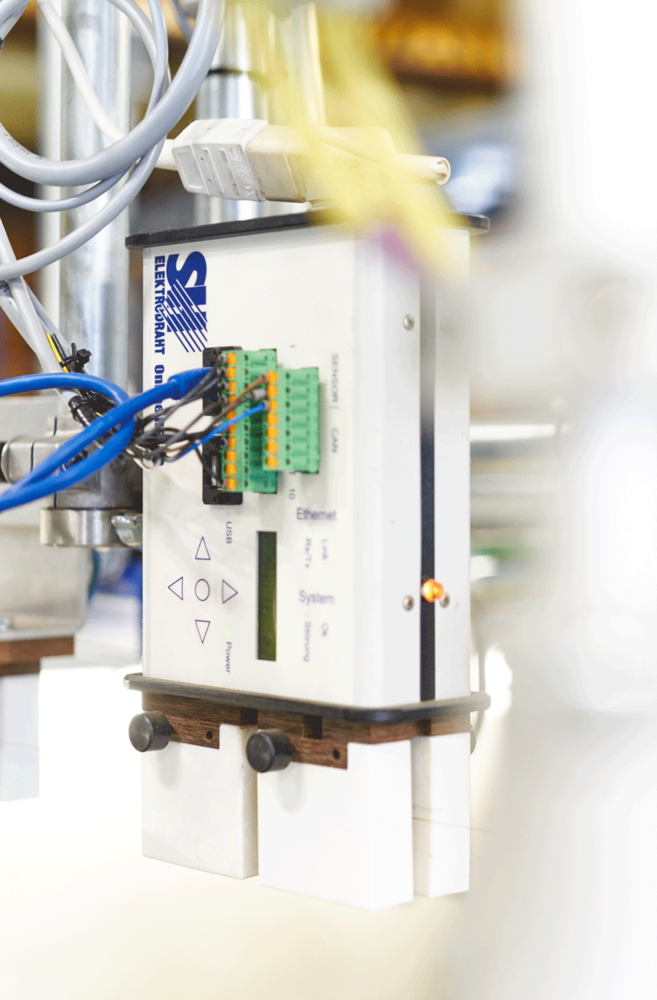
The term „Industry 4.0“ originates from a high-tech strategy project of the same name initiated by a research union of the Federal German Government. Industrial production is to be linked with the latest information and communication technology. Technological basis are intelligent and digital network systems. Using these systems allows mostly independent production: humans, machines, equipment, logistics and production directly communicate and cooperate with Industry 4.0. Based on closely linked networks it is to optimize more than just one stage of production, but the entire value-added chain. This network is also intended to capture all phases of products‘ life cycles – whether first vision, development, use, maintenance or recycling.