Self-bonding wire SHBond® from SHWire
What is self-bonding wire?
Self-bonding wire is characterized by an additional outer layer made of polyamide-based self-bonding varnish. Under the influence of heat this layer is activated, softened and thus becomes ductile. On cooling, the varnish layer solidifies again and forms a firm mechanical bond. The name self-bonding wire therefore refers to this special feature: the wire ‘bonds’ in the winding process and enables coils without core (air-core coils), for example, without any other auxiliary materials. The result is improved electrical properties, mechanical resistance and simplified production of windings and coils.
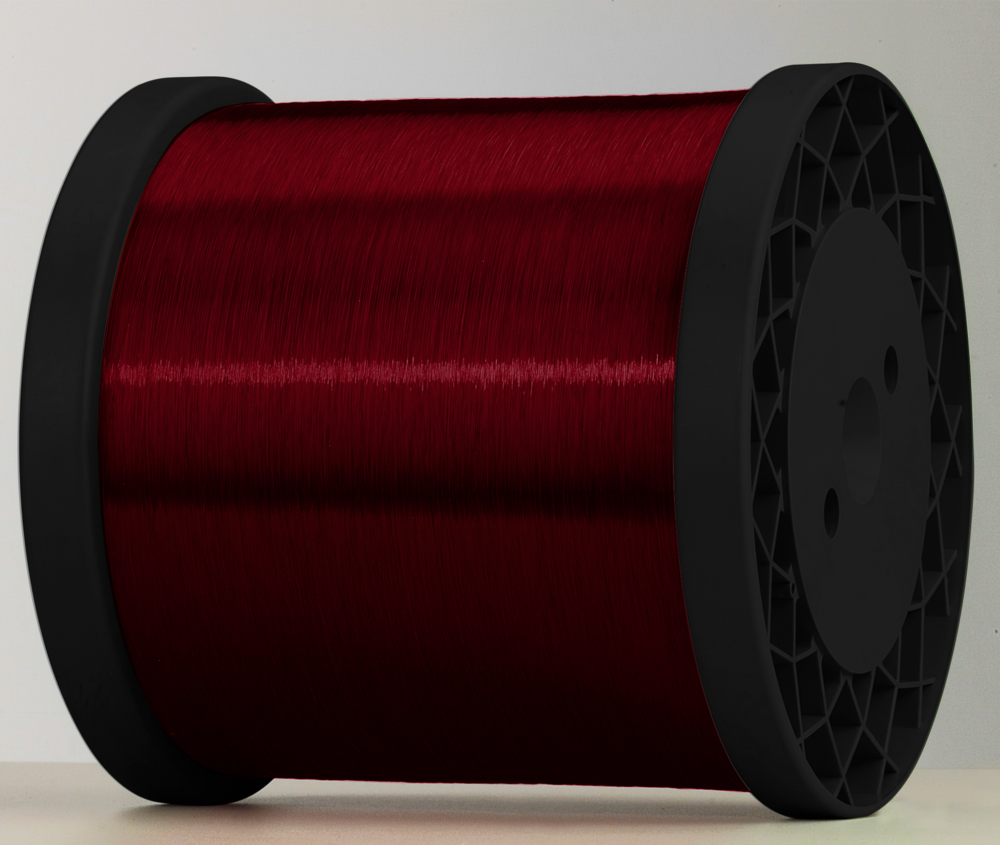
The advantages of SHBond® self-bonding wire
Our „SHBond®“ - selbonding wire offers numerous advantages:
- Winding without core: ductile when heated, stable and firm after cooling, allowing self-supporting and space-saving windings to be produced.
- No additional process steps/ auxiliary materials required: adhesive tapes, impregnating agents or potting compounds are not needed.
- Mechanical stability: greater resistance to mechanical loads, including shocks and vibrations.
- Highly heat-resistant: the 3-layer structure based on modified aromatic polyamides enables windings exposed to high thermal loads (thermal class N / 200) and fulfils the temperature index.
- Chemical resistance: additional protection against chemical influences.
- Less handling: the elimination of classic impregnation means that there is no curing time what enables faster integration into the production line.
- Environmentally friendly: the use, storage and disposal of certain volatile organic compounds (VOCs) is not applicable.
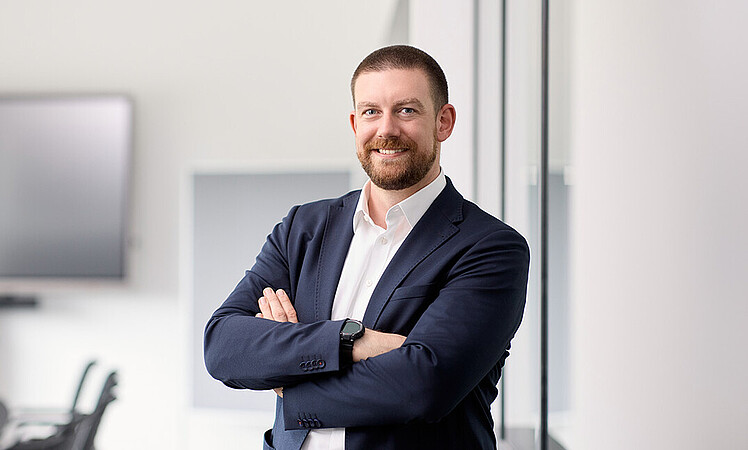
Find out more about our high-quality SHBond® self-bonding wires and how they can make your production more efficient and environmentally friendly. Contact us today for personalized advice and a non-binding quote.
Jan Oderwald
Head of sales
+49-5281-988-125j.oderwald@sh-wire.de
The SHBond® self-bonding wire portfolio
A characteristic feature of our self-bonding wire series SHBond® is the special 3-layer composition. This structure, which is unique on the market, combines the outstanding resistance and insulation properties of the SHTherm® 210 dual-coat with the special application options of the thermally bondable additional varnish coating based on mod. aromatic polyamide.
All SHBond® enamelled copper wires comply with the standards of IEC / DIN EN 60317-38 and NEMA MW 102-C.
SHBond® aluminum enamelled wires are analogous to IEC / DIN EN 60317-38 and comply with the NEMA MW 102-A standard
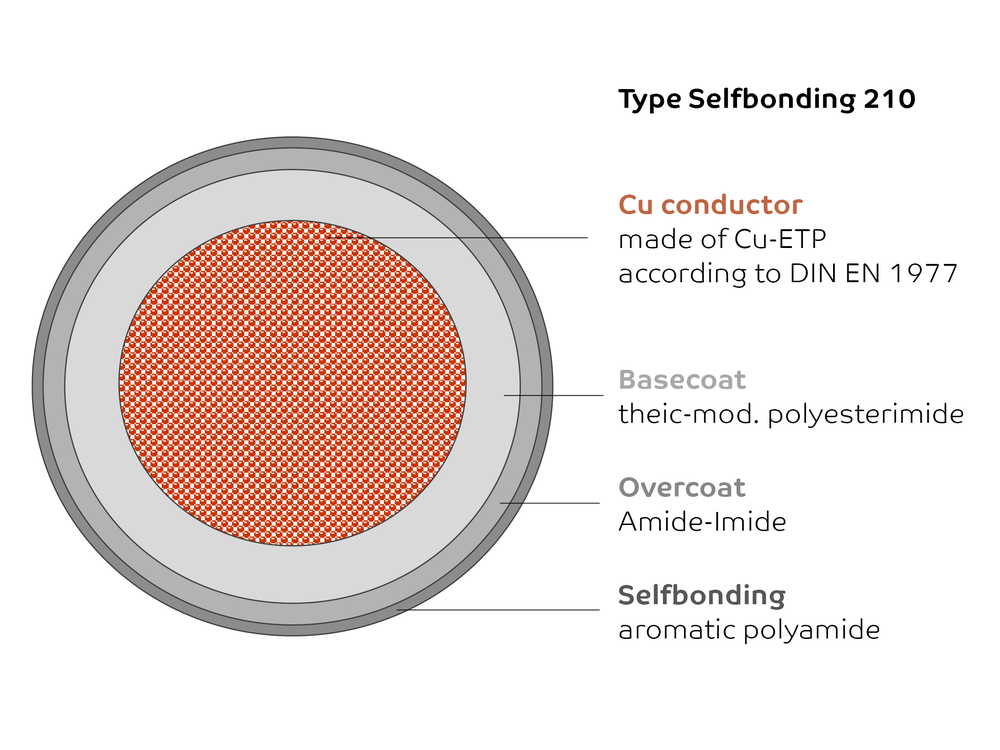
SHBond® WD 210 is our standard product for versatile applications. This wire offers excellent adhesion and insulation, ideal for transformers and electric motors.
Advantages:
- High thermal resistance (thermal class N / 200)
- Excellent mechanical properties and good chemical resistance
- Versatile use in various industries
- UL listed
SHBond® WD 210 Glide was specially developed for applications that require low friction which is usually no explicit advantage of a self-bonding functional coating. In this case, the final coating layer is designed as a low-friction functional layer and ensures excellent twistability, maximum slot fill factor, optimized winding speed, reduced system contamination and lower mechanical stress during the winding process. The reduced coefficient of friction results in more gentle wire processing which has a demonstrable effect on the insulation properties of the coating film.
Advantages:
- Optimized gliding properties
- Reduced friction during processing
- Ideal for complex winding processes
SHBond® WD 210 Alu
offers all the advantages of our standard wire, but has been specially developed for applications with aluminium. This wire combines the excellent adhesion of enamelled wire with the specific requirements of aluminium windings.
Advantages:
- Specially for aluminium windings
- Excellent adhesion and insulation
- Excellent formability of the winding head
Bonding options of SHBond® self-bonding wire
The self-bonding layer on the surface of a self-bonding wire is usually activated by heat. Here are the common bonding methods.
Thermal bonding
Bonding by means of hot air:
Hot air is directed onto the wire during winding what softens the self-bonding varnish and bonds the wires to each other.
Furnace bonding:
The wound coils are heated to a suitable temperature and remain in the furnace for a certain time to achieve uniform heating and bonding.
Resistance bonding:
Electric current is applied to the finished coil to heat it to the required bonding temperature due to the resistance of the coil.
Bonding with heated forming tool:
Self-bonding wires can also be partially bonded. For example, heated tools are used to form the winding head.
These bonding methods offer flexible and efficient options for reliably connecting the wires to each other and achieving the desired properties of the windings and coils.
Why SHWire?
- Experience and expertise: SHWire is your reliable partner with many years of experience in the production and development of enamelled wires.
- High supply availability: with Europe's largest production facility for enamelled wires, we can guarantee you high availability and short delivery times.
- Patented quality: our highly automated production technology and real-time monitoring guarantees highest quality standards. Every centimeter of wire is continuously monitored.
- Customized solutions: we offer customized solutions that are precisely tailored to your needs.
- Innovative technologies: through continuous research and development, we are constantly setting new standards in the production of enamelled wires.
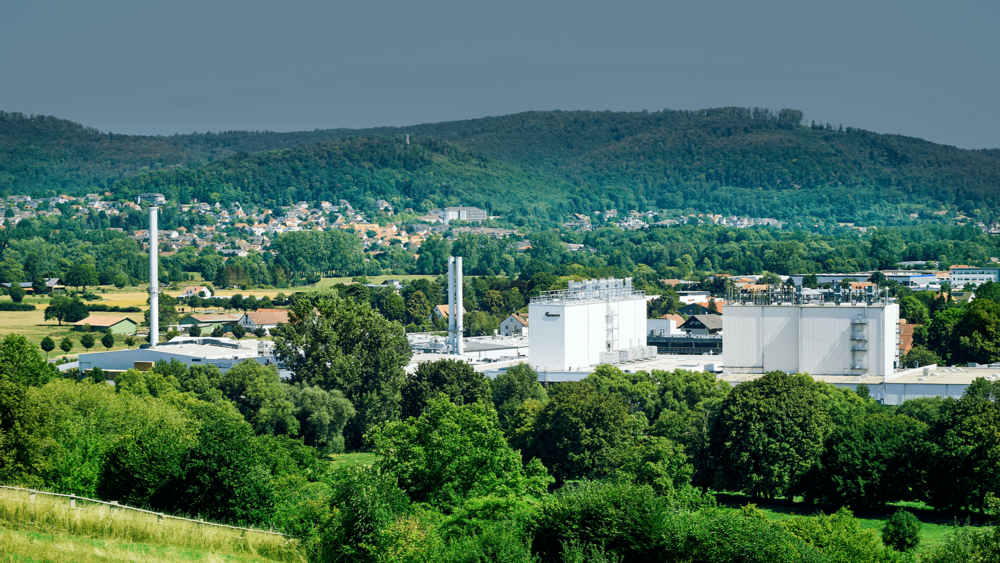